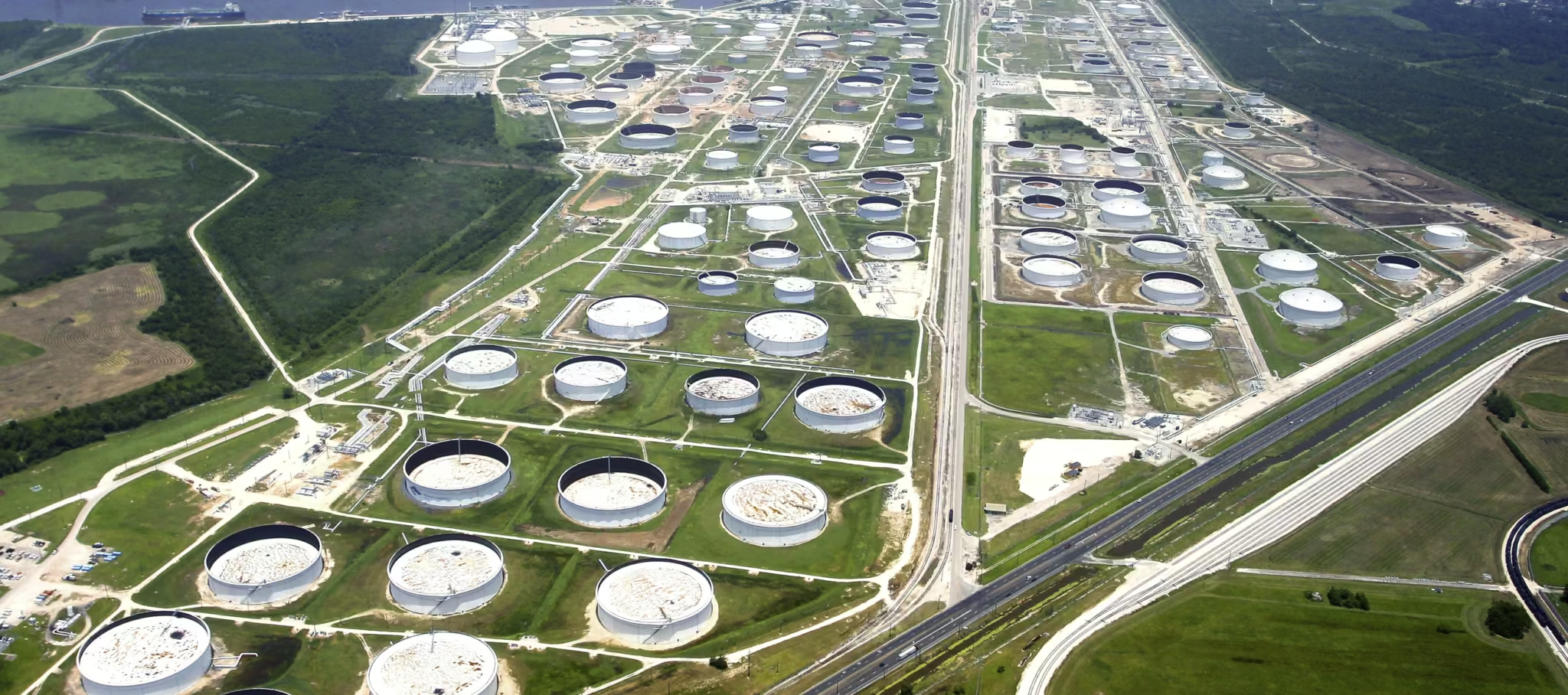
Tank gauging & loss control
Over 40 years ago, Gauging Systems Inc. (GSI) started as a scrappy service and repair team, diving deep into the world of tank gauging with a relentless drive to solve real-world challenges. We didn't just fix systems-we studied them, uncovered their flaws, and dared to dream bigger. That spark of ingenuity ignited a revolution, transforming GSI into a trailblazer in the tank gauging industry. From inventing the game-changing MTG “Multi-function Tank Gauge” to pioneering the MMP “Multi-Media Probe,” we've redefined precision, safety, and efficiency for bulk liquid storage. Our cutting-edge solutions slash costs and elevate performance, making us the go-to partner for petroleum, petrochemical, and beyond.
Our offerings cover the full spectrum of tank monitoring and production needs:
- Liquid Tank Gauging (product quantity and quality)
- Overfill and Rupture Protection
- Leak Detection (unauthorized product movement)
- Vapor Monitoring (emissions, PRV, and blanket systems)
- Tank Bottom and Roof Movement Detection
- External Floating Roof (EFR) Water Accumulation Monitoring
- Mixing Optimization and Electrical Savings
- Communications HUBs (bridges legacy or competitor gauges)
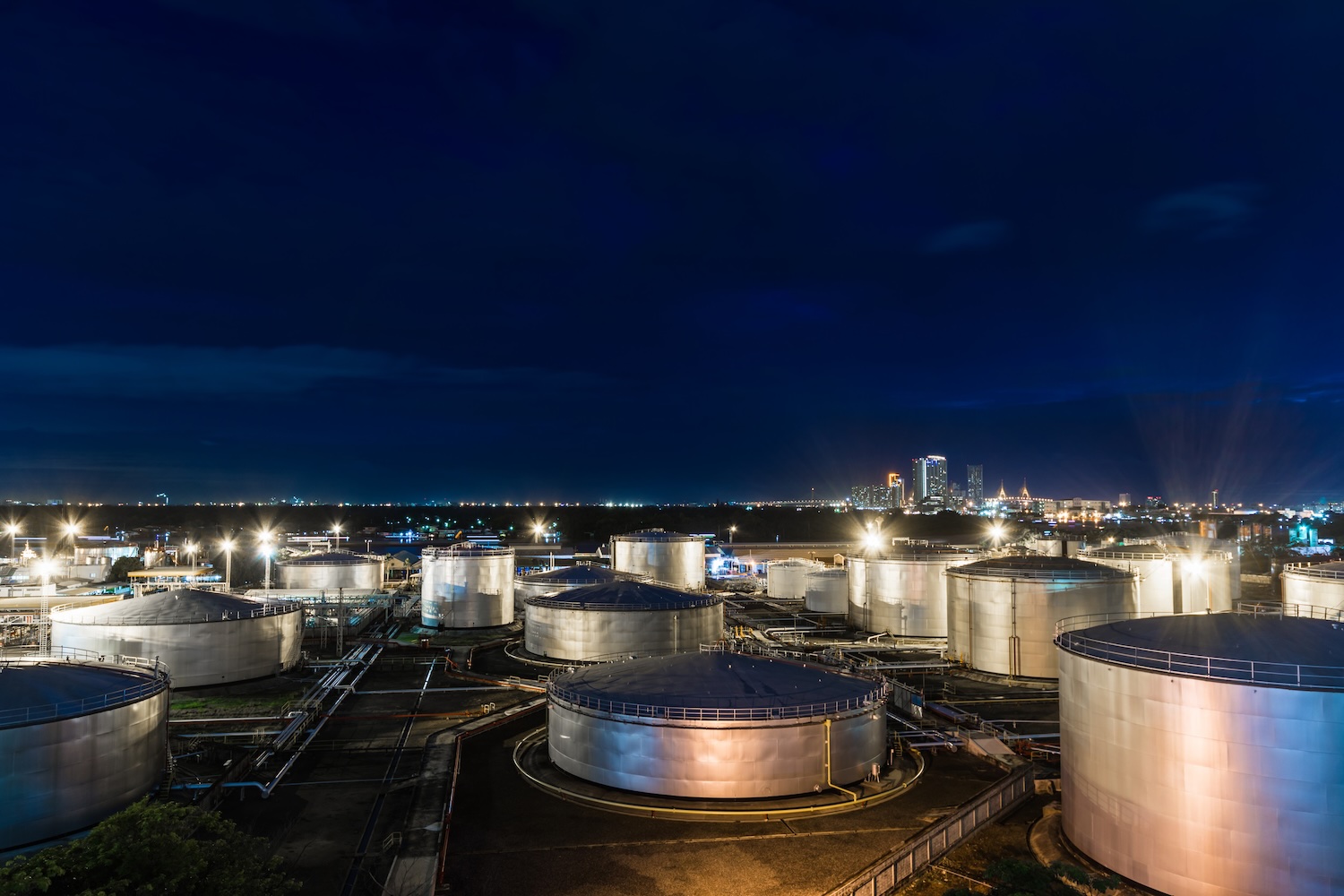
Welcome to Gauging Systems Inc.
A comprehensive set of services
Support of Existing Systems and Equipment
Gauging Systems Inc. (GSI) delivers top-tier tank gauging services, leveraging 40 years of expertise. From our roots in field and bench repair, we maintain the industry's most experienced staff and service contracts for all major systems and technologies from the past 50 years.
New Systems and Equipment
Additional services include system specification, manufacturing, testing, integration, system staging, topology configuration, software and network configuration, internal testing, and system documentation, ensuring complete support for all major systems and technologies
Engineering Services
By addressing challenges like technology misapplication, liquid-specific issues, and improper installations, we've developed advanced tank gauging solutions for superior performance and reliability. Our expertise informs innovative product design, precise installation techniques, and comprehensive training.
Revolutionizing Tank Gauging with Passion and Precision
At GSI, we don’t just lead—we innovate relentlessly, delivering turnkey solutions that empower our global clients to master inventory control with unmatched confidence. Join the revolution with GSI, where bold ideas meet unparalleled expertise!
Services
We provide: Both bench and field service repair of tank gauging and related equipment. Project engineering and supervision for on-site installations (retrofit or new equipment). Engineers (Communications, Electrical, Mechanical, and Software) available for system design and custom (OEM) product design.
Software
GSI provides: “TG SOFT SERVER” software for Inventory Monitoring, Tank Gauging, Overfill & Rupture protection, Leak detection (Continual and tank tightness testing), and various applications for Vapor and Ambient Air Monitoring. Distribution and Pick-up Systems for various commodities.
Instrumentation
Gauging Systems Inc. (GSI) manufactures: Flood Gauges, Target Boards, Sump Gauges, Level Indicators, Tank Gauges, Mechanical Float & Tape Gauges, Multi-function Tank Gauges, Digital Transmitters, Analog Transmitters, Limit Switches, RTU’s, LPG Tank Gauging, Communication Interfaces, Solar Interfaces, Instrument Shelters, High Level Alarm Switch, Overfill and Rupture Prevention, Unauthorized Movement Alarms (Leak Detection, Theft, Improper Line-ups, Equipment failure, etc.), and more.